
Automated Test Systems
Custom automated test systems to support your product development.
We provide turnkey automated test systems for product development companies in both research & development and manufacturing production environments. Our small, focused team provides quality solutions with aggressive lead-times and competitive pricing, providing most RFQ proposal responses within just a few days.
With Novum Automation, the development of your automated test solution is thoroughly managed from start to finish. Each project begins with a schedule that defines all tasks and milestones, outlining any critical paths or areas of concern. Project updates and weekly meetings are provided as requested to promote cross-functional visibility and unparalleled organizational efficiency.
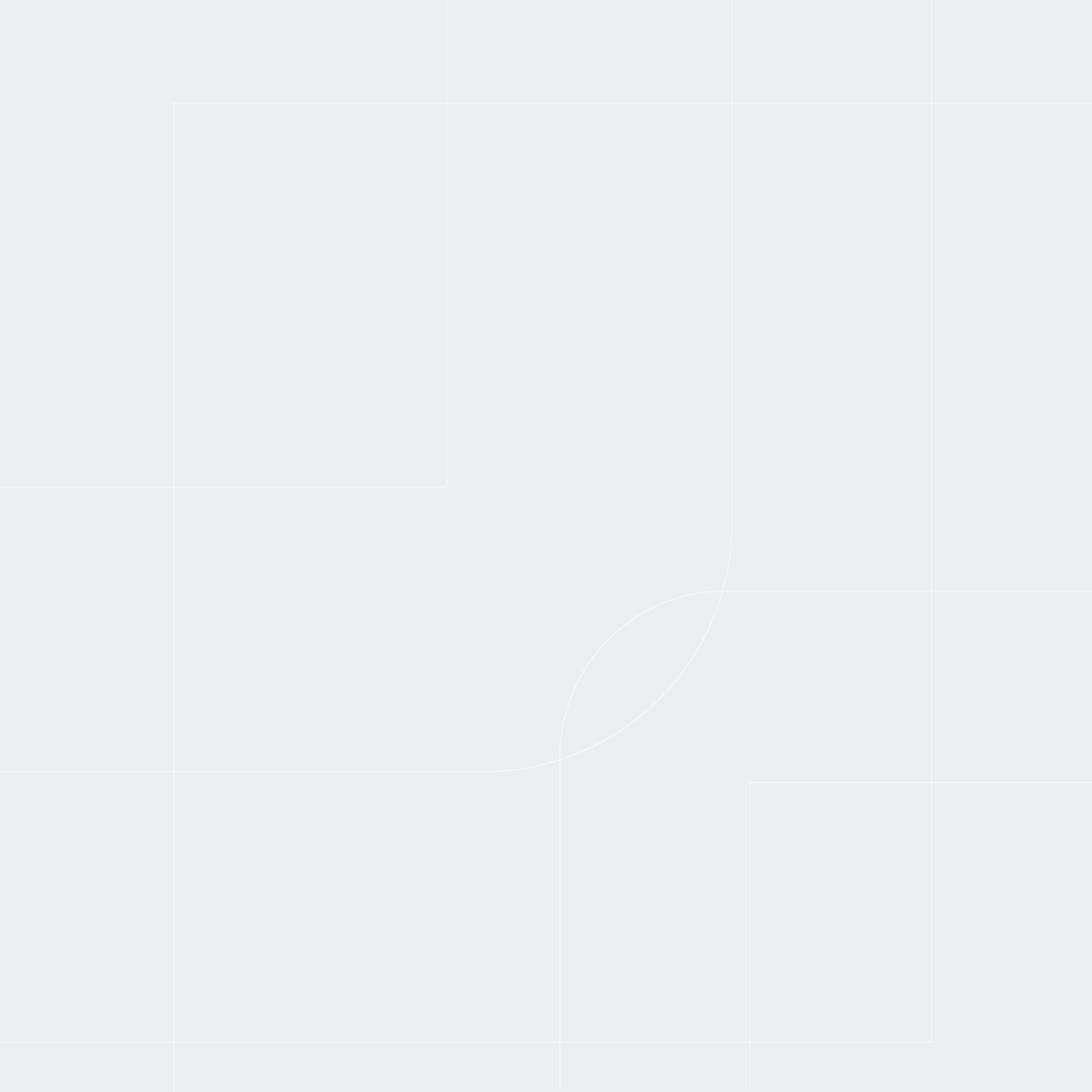
Research & Development
Automated quality inspection equipment
R&D lab equipment for product durability & performance testing
High-Speed data acquisition and control hardware systems
Electrical control panel design and wiring
National Instruments LabVIEW software programming
Validation testing systems for repeatability and reproducibility
In-Line Manufacturing
Automated in-line quality inspection equipment
Vision system integration for part inspection
Data integration with existing database architectures
Collaborative robot integration for automated test or inspection cells
Rapid production part validation testing systems for repeatability and reproducibility
Turn-key Test Systems
Comprehensive automated test development services covering all aspects of system development (scope of work, design, procurement, build, assembly, wiring, programming, and validation)
Software development (NI LabVIEW, Python, Allen-Bradley RSLogix, Siemens TIA Portal)
Electrical control panel design & development
Mechanical part & test cell fixturing design & fabrication
Recent projects

Learn more about our methodology.
Customer testimonials

30 Year old control system was becoming unreliable and costly to maintain. Novum fully upgraded electrical enclosures & custom LabVIEW software.